DIGITALISING THE DESIGN PROCESS- HOW CAN WE HELP IT TO HELP US?
- johnrisley3
- Dec 3, 2022
- 10 min read
Updated: Feb 20
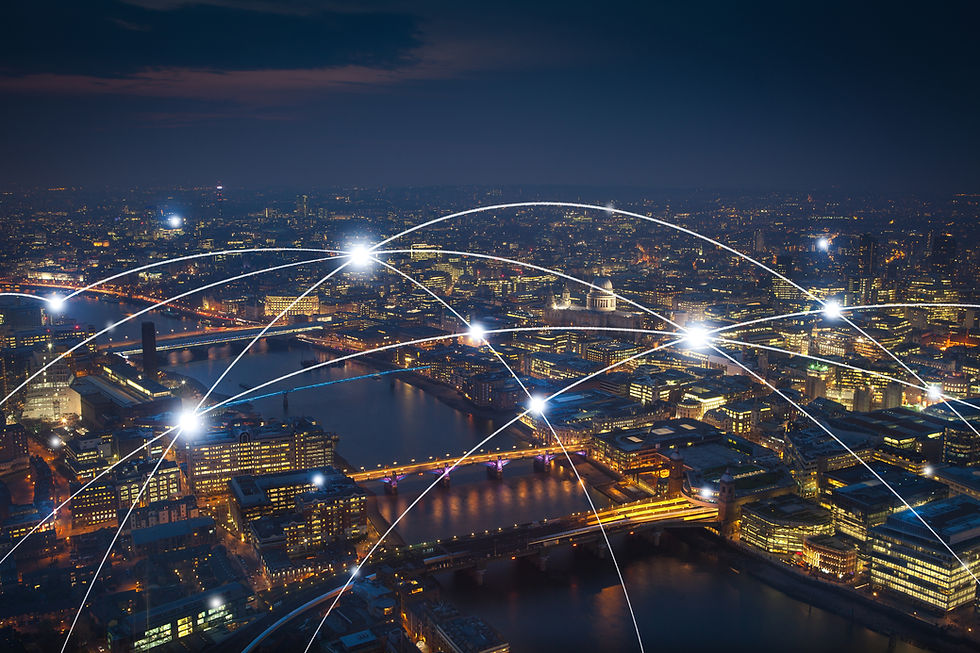
We have all heard how digitalisation is going to revolutionise the construction industry, it will apparently increase our productivity levels and wave a magic wand over the industry’s problems. However, reality is never as simple as the soundbite. Big data and digital design can make significant contributions in the rationalisation and optimisation of our approach to building design, but technological change is not an independent variable. Whilst technology will advance, often in surprising and unpredictable ways, its overall trajectory is defined by economics and legislation.
McKinsey research has shown that in the 20 years to 2015, manufacturing productivity rose by 30% in the UK, compared to a 7 % increase in construction. A significant part of this is through efficient implementation of technology in design and delivery, something we have yet to see in the built environment. We here at London Structures Lab encourage the definition of outcome- and result-orientated processes. Whilst technology has and continues to help the construction industry streamline and innovate, we are yet to see productivity impacted in the same way as other sectors. Here we look at why that is and what steps can be taken to enable the potential of digital processes.
What is digital design?
Digitalisation means different things to different people. We would say that it is a wide-reaching umbrella term covering the use of technology, both software and hardware, to do tasks that have traditionally been performed by hand. Within construction, this means anything from automating the sizing of beams to reduce the need to do a hand calculation for each one, to using electronic monitoring points on site connected up to an automatic trigger system that alerts the contractor when excessive movement occurs during construction.
Whilst London Structures Lab can have our biggest impact in design, bringing our knowledge of the full construction process is essential to adding value at the beginning of any project for our clients and collaborators. Therefore, for us, digitalisation is primarily about when, how and why we use digital tools during the design of a building, and where we might introduce data-driven design to create material efficiency, design quality, improved communication and enabling improved health and safety approaches.
Where is technology being deployed and where is its impact limited?
Is it right to directly compare the productivity of construction, where every building is a prototype and countless stakeholders form a new team for every project, to manufacturing, where the same product is fine-tuned and mass produced in a single controlled location?
Frequently “optimisation” refers to minimising the material required to achieve a pre-determined volume and form. When we say “the-form-was-optimised-to-minimise-the-embodied-carbon-used” should we honestly be saying “the-spatial-requirements-determined-by-the-viability-model-which-had-been-signed-off-by-the-funders-was-optimised-to-minimise-the-embodied-carbon-used,-in-an-exercise limited-to-an-assessment-of-this-building-in-isolation.-Factors-such-as-global-material-availability-and-competing-developments-proposed-material-usage-were-excluded-from-the-exercise”.
Here at London Structures Lab, we are not interested in productivity in terms of churning out more buildings per person (though we are aware that we have an industry skills shortage that technology can assist in addressing). We want to use the most appropriate tools on each project to ensure we minimise material use, minimise time on site, maximise reuse of existing building material and perhaps most importantly, improve safety on site. We always believe there is a better way to do something. Upskilling the sector in digital assessments, used with open and honest expression of their limitations, is essential in addressing the climate crisis. By combining the right digital tools with our practical experience, we aim to maximise the value we can add to any project.
How do engineers implement digital design now?
Due to legislation on public sector projects, the industry is moving towards BIM literacy. This means that most large-scale projects are now delivered with associated 3D models from each discipline that can be combined to give a digital version of the project. This offers benefits from early design coordination between disciplines to avoid clashes on site, to allowing subcontractors to prefabricate building components to increase quality, speed up the site programme and reduce waste.
These benefits are made possible by the digital creation of many thousands of data points for the project. The digitalisation of this data opens up countless opportunities. The amount of data increases as a project develops. The initial concept phase has a small quantity of data, or known knowns, with many unknowns.
Once these principles are understood, we can start to generate data, from the geometric constraints, to applied loading, to total floor area. Using this data, we can use the most appropriate tools, digital or manual, to evaluate possible solutions to the problem in question. One such tool is computational software, which add detail to possible solutions, or find further solutions that weren’t previously intuitive, this may provide us with valuable insight for our designs.
By appreciating that data can provide the skeleton for any models we create, we can shape our approach to the BIM process, to aid design, analysis, coordination and communication as required at each stage of a project. We ensure that we agree our workflow at the start of the project, so that the right tools are used at the right time. The use of digital tools to manipulate data where this is more efficient leads means that work is neither abortive nor repetitive.
We utilised the following approach on a recent retrofit project to maximise the use of an existing asset.
Design occurs as a collective
Baseline structural model is created via a script in 3D CAD software (Rhinoceros)
Data is extracted using scripts in computational software (Grasshopper or Dynamo)
Data is transferred into either Excel for processing or directly into Revit
Data is pushed into one of a number of analysis packages to analyse the structure and develop the design where required
Once the analysis is completed, the geometry can be pushed back into Revit with relevant properties assigned to individual structural components; these can be directly shared with contractors for components they are to design
The Revit model is then developed during coordination with other disciplines and more detail added to generate the final construction delivery model
Upon completion of the project, the model can be used to identify residual capacity and opportunity for future expansion or alteration- usually provided to the client in a future proofing report

As our recent thought piece on the use of technology in refurbishment argues, we actively support and promote refurbishment as a viable option to maximise the value of a client’s existing assets. To achieve this, it is vital that we communicate different building massing, grid and material options to the client and architect at an early stage. Existing building information can be piecemeal from record or survey, and to unlock this, an efficient workflow is required to convert this data into a 3D format.
The above workflow was adapted on a recent commercial office in London. The basis for both our analysis and delivery was the existing 2D information. The building was built in the 1890s, mostly rebuilt in the 1930s, and again in the 1990s with only the 1930s masonry façade, heritage staircase and Victorian vaults retained. The largely new-build 1990s existing frame was digitalised using computational software Dynamo. We developed a workflow which takes CSV data of member locations of structural frame and pushes this into Autodesk Revit. Using our in-house Revit template, the software simultaneously creates both the BIM model for coordination and an analytical model of the frame, which can be exported to Autodesk Robot or Tekla Structural Designer.

This saved set-up time, with the final construction delivery model and analytical models synchronised. This enabled optioneering with the architect and visualisation of issues to maximise the reusable floor area, minimise the embodied carbon of the building and minimise the build time.
This is just one example of how working in a multi-functional 3D environment at all stages of a project offer far more benefits than just design efficiency. At an early stage, 3D information can help to communicate design options and their implications to clients. For retrofit, we can highlight site constraints or which parts of the existing structure that will need strengthening for any additional number of storeys on top of an existing building.
What are the current limitations of digital design?
Whilst increasing number of engineers are computer literate, senior members of structural engineering companies, clients and other stakeholders do not often fully understand the possibilities and limitations of digital tools. Therefore, those setting out the high-level project plan at an early stage may not be fully aware of the possible workflows. This can lead to over or underestimation of capability. Developing detailed 3D models too early in the project, thereby wasting time with no meaningful output, or not appreciating a project’s potential for 3D coordination or automating design, does not advocate the process. It is critical that all members of a design and construction project team have a basic level of digital literacy to take full advantage of the project’s data.
Although complex scripts can solve complex problems, they are easily poorly designed for future adaption and illegible to the layman. It is the responsibility of those within an organisation with the know-how to create programs that enable the team and clarify rather than mystify the process.
In recent years the term artificial intelligence and optimisation have been mindlessly applied to solve various problems to create the illusion of value created by the engineer. This is often directed by management staff who are more concerned with the marketing of the company than the production of efficient solutions. Artificial intelligence is a non-convex optimisation process, often with multiple objectives to minimise or maximise, which do not always pull in the same direction. Because of the competing forces at play, the means of arriving at a solution is not inherently obvious to a heuristic solving algorithm. It should be noted that there is no guarantee that an ‘optimal’ solution provided by an engineer is ever truly optimal. In summary, there is no replacement for a firm grasp of the preliminaries in physics and mathematics when it comes to providing solutions using computers.
What are the opportunities of digital design?
One thing computers do have over humans is the ability to store hundreds of thousands of data points. On top of saving analysis models so that we can go back to them at a future date, this offers the much bigger potential for the BIM model to store all kinds of metrics about a building for years to come. This then feeds back into our pool for data driven design approaches.
Specifically to structures, we can ensure the geometry and material properties of all elements are captured in our BIM model. By providing the client with this model and so information, we are enabling them to undertake future building alterations with their eyes wide open and so from a much stronger starting point. In this way, we can reduce barriers to both refurbishment of existing buildings and the reuse of individual components at the end of the useful life of the whole building. Therefore, we increase the scope for future embodied carbon savings after the useful life of this refurbishment has expired.
The use of the 3D BIM model with stored information for each elements also increases the scope for prefabrication in the initial construction process. It enables procurement of structural elements directly from the model, ensuring prefabrication can occur in the knowledge the design is coordinated. The elements can then be erected on site with mechanical connections, reducing waste and wet trades on site, reducing programme.
Clients do not yet value this BIM information in terms of willingness to buy it. However, a current London Structures Lab refurbishment in the City of London clearly demonstrates current BIM information’s future benefit of removing the risk associated with unknowns and the time and cost of investigations. Without the existing information on the structure and with time constraints on investigations, around 5% of the floors we are retaining would have had to be flagged as preliminary demolition on contract drawings. This risk would have been allocated a price, which would have eroded profit. Furthermore, we can use information such as cube tests for concrete and instrumentation of existing foundations to inform assessment of the true building capacity.
Next steps
Whilst UK legislation, such as the 2016 BIM mandate and government contractual requirements, has made some progress towards improving building data recording, the economic imperative has not been there for a cohesive industry drive. Things are best adopted when the person paying for it has the expertise/control to reap the reward, hence steel fabricators were the natural early adapters for their own benefit. However, the economies are currently limited to internal company efficiency, as the saving has been design professional’s manpower, with the cost of materials and physical labour remaining relatively unchanged.
The myriad benefits that the use of digitisation of data offers can only be realised when the construction industry has the collective capability and truly works together. Legislation can provide the step change that is needed. It is no good one consultant or contractor pushing technology ahead in a silo, if others do not see benefit. If the contractor is set up to take the structural engineer’s BIM model to maximise and speed up prefabrication, but the structural engineer has not included enough information in their BIM model, the contractor wastes a lot of time and effort. If the structural engineer provides the client with the BIM model for future alterations, but the client does not have the literacy to open and use this model, the benefits are lost.
Until legislative influence can provide a unifying cross-industry benefit through more intelligent funding assessments, or further material cost inflation demonstrates greater impact, the development of the tools and the upskilling in this area will not be a coordinated, whole industry focus.


As we mentioned at the start of this thought piece, productivity in construction is lagging behind other industries. Despite technology being available to all industries and adopted in many ways in construction, why has it not led to tangible productivity improvements? The digital tools now available to speed up basic tasks that don’t require human input, we could be producing the same buildings but more efficiently and cheaply. Instead technology has been used to complicate either the analysis process or the end form. Neither a good use of time or money, not to mention the wasteful use of materials that is linked to inefficient structural forms. For embodied carbon and cost, we should all be aiming to build less. Efficiency of form and load path are two contributing factors in this.
We believe digitalisation across the industry offers construction, supported by government initiatives like the Construction Playbook and the Value Toolkit, give us the chance to finally make a step change in collaboration and the associated productivity that have been promised for so long. However until the influence of these hits the private sector, through filtering through from government procurement process- which will take time. It is up to all of us to work together, discussing openly and honestly, to ensure that we all benefit from our individual technological advances.
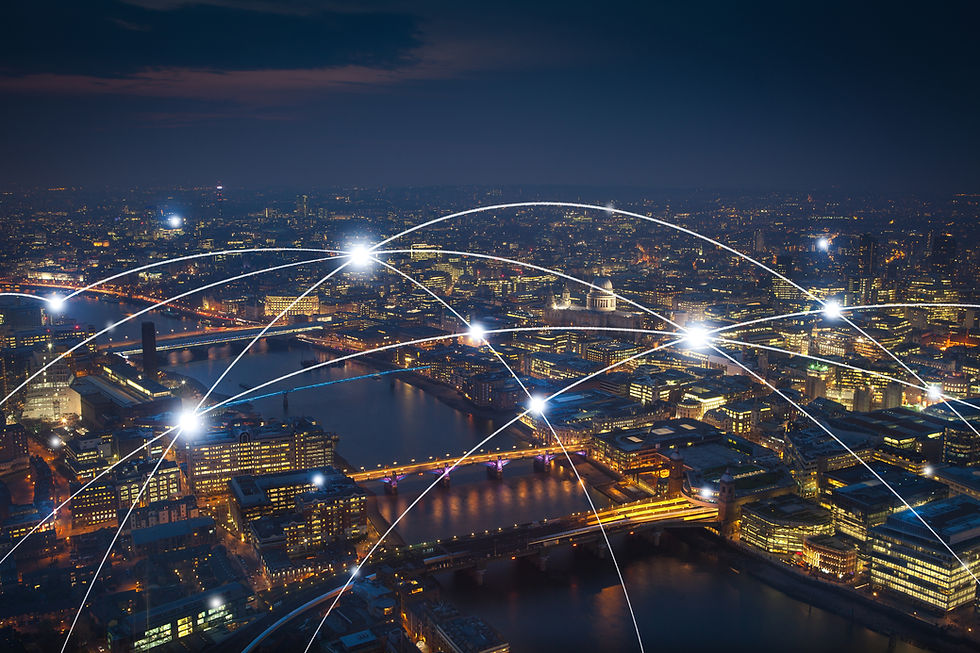